The main energy source used to process EPS foam is dry saturated steam, if superheated steam is used will make the product surface quality and melting effect is poor, sometimes the product will break. If the use of wet steam will make the product in the moisture content is too high, the production cycle has cooked, the time required will also be extended. The easy way to detect the moisture content of steam is to pull down the rubber tube received from the molding machine and exhaust it horizontally into the air, when the steam is ejected horizontally forward at the same time, observe whether the steam contains liquid water below and the parabolic trajectory of liquid water to determine the moisture content of steam.
If the water capacity in the boiler is not sufficient, a storage tank is required to discharge the steam required during the production period during peak production periods. The amount of steam required for each machine, such as preformers, sheet molding machines, packaging molding machines, etc., should be calculated separately and summed up.
The steam pressure in the mold cavity is 0.1~0.2MPa as required by the molding process. It is also required that the pressure be stable and that the steam contain little water. For the steam pressure generated by the boiler is 0.6~0.7MPa or even higher, so a pressure reducing valve should be installed in the piping before the molding machine. Of course, the amount of steam from the boiler must meet the entire production of gas needs, steam inlet pressure of 0.5MPa, pre-generator and fluidized dry bed steam receiver for DN20, gas consumption are 90Kg / h.
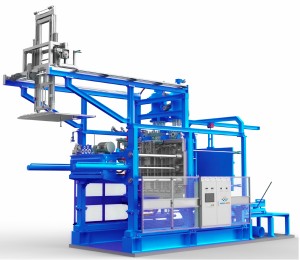
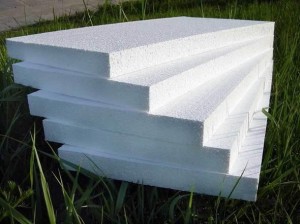
For low energy-consuming equipment, if the daily output is 1.8~2t, it is more appropriate to choose a boiler of 1~2 t /h. The location of the boiler room should be as close as possible to the center of the production heat load.
The steam piping in the boiler room includes the main steam pipe and the sub-steam pipe, the main steam pipe is used for external gas supply, the sub-steam pipe is used to supply steam pump gas, sootblower gas and other boilers for their own steam, the boiler room is equipped with many types of valves, safety valves, drain valves, check valves. Other valves commonly used in steam systems are ball valves, gate valves, throttle valves, etc. Among them, the safety valve is an important safety accessory on the boiler*. It plays an important role in controlling the ultimate pressure inside the boiler and protecting the safety of the boiler. When the pressure inside the boiler rises above the specified value, the safety valve is automatically opened to discharge a large amount of steam to the outside, when the pressure inside the boiler is reduced to the specified value, the safety valve is automatically closed. Improperly configured safety valves, or not used in accordance with the provisions of the boiler is easy to overpressure resulting in an explosion accident.
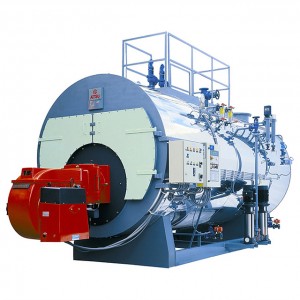

From the EPS molding production in practice, as each machine is intermittent gas, which causes the amount of gas is extremely uneven, with a certain size of the EPS molding plant should be installed with a steam accumulator.
Steam accumulator is saturated water as a medium to store heat pressure vessel, its upper part is filled with saturated steam, the lower part is filled with saturated water. When the pressure decreases part of the saturated water vaporization for steam water level drops, the accumulator outward heat release. Conversely, when the pressure rises, part of the steam into saturated water level rises accumulator heat absorption.
Post time: May-22-2023