EPS lost foam mold, is a process that uses foam plastic patterns instead of traditional patterns to compact the mold. After the mold is made, it does not need to take out the pattern, and you can directly pour liquid metal into it. Under the effect of high temperature liquid metal, foam mold will be vaporized by high temperature, and then will burn away, The metal liquid will replace the space occupied by the original foam plastic mold, and after cooling and solidification, the castings needed by the EPS lost foam mold can be obtained.
Lost foam casting is a very advanced modern casting process, and many manufacturers have started to invest in it. So what are the advantages of lost foam casting?
1. Lost foam casting can greatly reduce production costs;
2. Manufacturers can use the lost foam casting process to complete castings of any size based on their melting ability.
3. The lost foam casting process is widely used, not only for casting steel and cast iron, but also for casting copper and aluminum, and so on.
4. Lost foam casting manufacturers can not only use castings with relatively simple geometric shapes in lost foam casting, but also make castings with complex geometric shapes with multiple edges and cores that are difficult to use in ordinary casting.
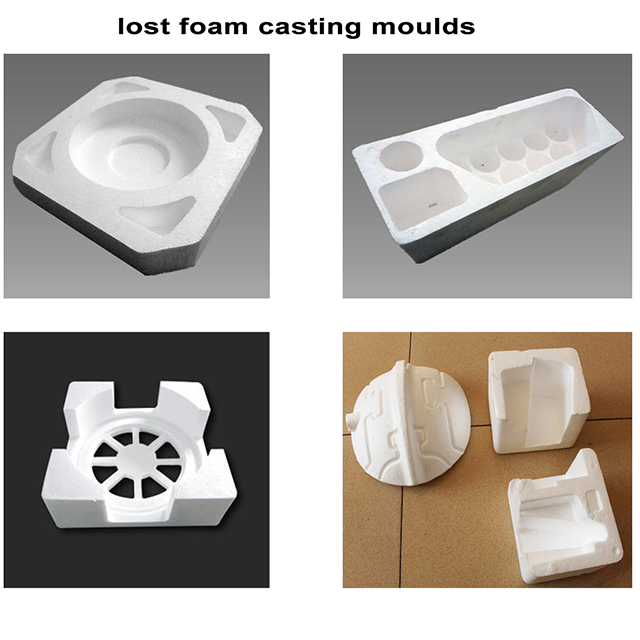
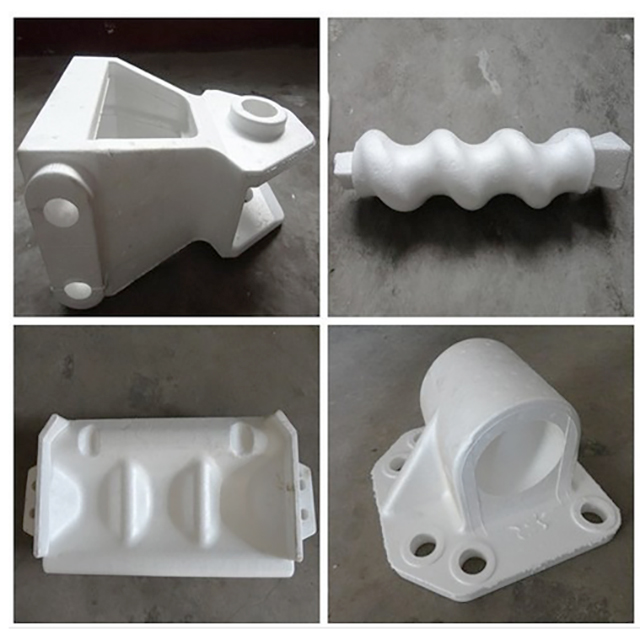
Post time: May-18-2023