EPP is widely used in high-speed railway, automobile and other industrial products, such as bumper core material, anti-collision block, roof and other lining parts, door filling, headrest, sunshade and so on, which can save fuel consumption and improve passenger safety factor.
EPP has been widely used in the packaging industry, such as electronic products, medical devices, etc., especially in the packaging of export products, it has become an irreplaceable packaging to meet the requirements of environmental protection. Due to its non-toxic and high temperature resistance, it is also widely used in food packaging and microwave heating.
Finally, EPP is made from high melt strength polypropylene (HMSPP) rather than ordinary polypropylene (PP).
General PP molecules are plain (neither fork) must go through a certain post-processing, so that its molecules into a fork, commonly known as PP graft (general graft degradation will occur, not to make it has high viscosity and high melt strength purpose). Generally, EPP beads should be loaded in the pressure tank first (even if the beads are filled with a certain pressure of air), and then injected into the mold of THE EPP molding machine with compressed air through the spray gun, through the steam to further expand the EPP beads and surface fusion together and forming. After cooling, the mold is stabilized at a certain temperature to obtain EPP products.
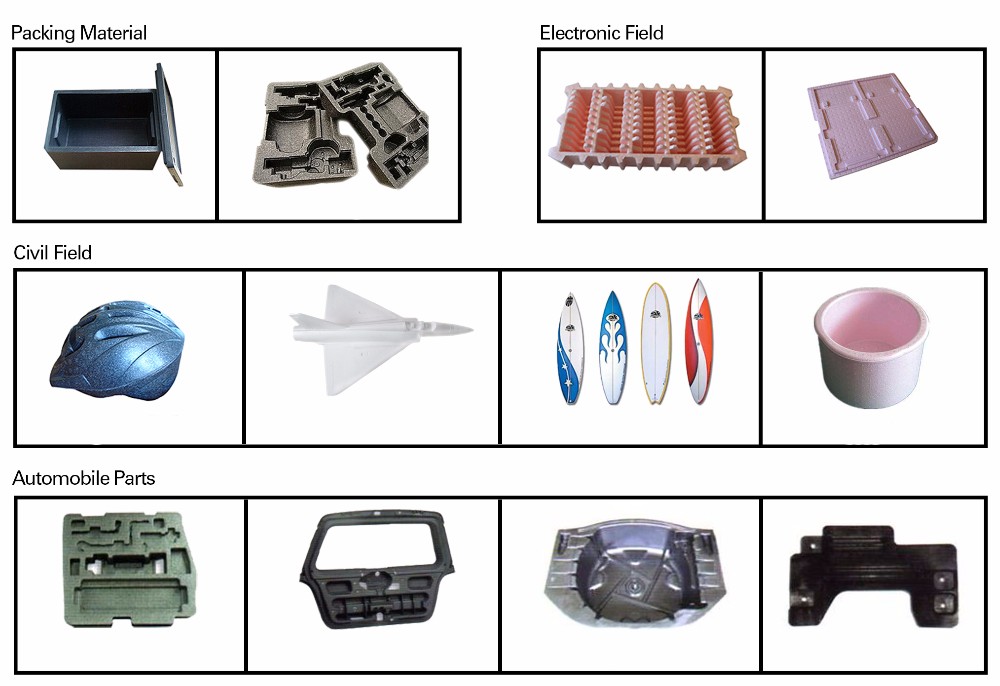
Post time: Jan-04-2022