EPS Underfloor Heating Panel Molding Machine
Main Advantage
Fully automatic EPS foaming mold making machine products are widely used in industries such as vegetables and fish boxes, electrical parts packaging, wall and roof insulation, and house decoration.
1. Machine with strong structure.
2. Use PLC and touch screen control, run automatically.
3. High efficient vacuum to make good quality products.
4. Use different operate language, more easy to operate for workers.
5. Two vertical hopper for filling material faster.
6. Use good quality parts.
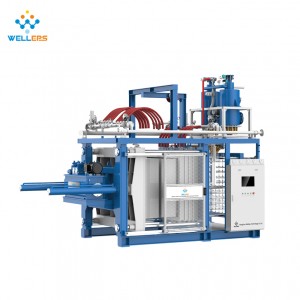
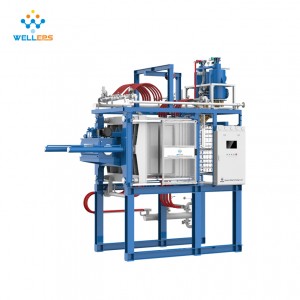
Machine Introduction
To accommodate with different sized product, the machine has a variety of templates, the smallest size is about 1400×1200 mm. The maximum size can reach 1800 × 1600 mm.This machine is equipped with two-step hydraulic system, compressed feeding system, and central energy system, relief damper, holding-pressure water tank, condensation system, computer-controlled system, digital process control system and steam room.
The vacuum system is equipped with the Liquid Ring Vacuum pump and condenser which provides more efficient vacuity. Without any extra drying step, we can speed up the injection under this vacuum system. The mold ejection is easy to be completed and also save the more energy.
The adjustment of energy pressure is very important. Under higher steam pressure, the production time will be prolonged and consume more energy. However, the final product might be deformed and the surface appearance of the product might be affected when the pressure is too low. The relief damper functions when releasing mold and heating up the mold. The compressed air is used for filling and this damper will reduce the consumption of energy and provide high quality product.
This machine has one full set of central energy system which is produced by our company All steam and air which are needed during the injection process are controlled by the central energy system valve. This system will provide even air intake and can be adjusted easier. This low-pressure steam system is designed with enlarged pipes and valves which can provide best working condition.
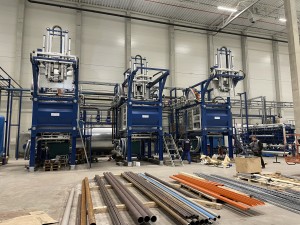
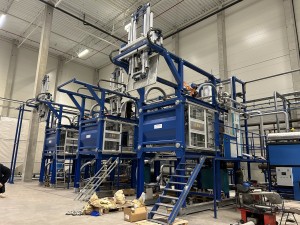
Technical Data
Item | Unit | EPS1412 | EPS1513 | EPS1816 | |
Outer size of mold | mm | 1400X1200 | 1500X1300 | 1800X1600 | |
Window size | mm | 1250X1050 | 1350X1150 | 1680X1450 | |
Final product size | mm | 1200X1000 | 1300X1100 | 1600X1400 | |
Max product height | mm | 400 | 400 | 400 | |
Steam system | Pipe connection | DN | 100 | 100 | 125 |
Mold connection | DN | 40X6 | 40X6 | 40X8 | |
Work pressure | Kg/cm² | >3 | >3 | >3 | |
Consumption | Kg/cycle | 3~5 | 3~5 | 4~7 | |
Air system | Pipe connection | DN | 50 | 50 | 65 |
Work pressure | Kg/cm² | >4 | >4 | >4 | |
Water system | Pipe connection | DN | 80 | 80 | 100 |
Work pressure | Kg/cm² | >3 | >3 | >3 | |
Mold connection | N | 25X6 | 25X6 | 25X8 | |
Temperature | ℃ | 40~55 | 40~55 | 40~55 | |
Drainage system | Vacuum connection | DN | 100 | 100 | 125 |
Fixed and moving mold drainage | DN | 80 | 80 | 100 | |
Drainage pipe connection | DN | 100 | 100 | 125 | |
Mold connection | DN | 40X6 | 40X6 | 40X8 | |
Hydraulic system | Oil pump motor | KW | 5.5 | 5.5 | 7.5 |
Oil pump capacity | L/min | 25/75 | 25/75 | 25/94 | |
Max clamping force | T | 24 | 24 | 38 | |
Pen and clamp oil pump | mm | 100X1360/2 | 100X1360/2 | 125X1360/2 | |
Demold oil pump | mm | 50X30X450 | 50X30X450 | 50X30X450 | |
Mechanic demold and hydraulic demold ways can be optional. | |||||
Bucket system | Bucket capacity | m³ | 0.15 | 0.15 | 0.3 |
Feeding fan | Kw | 1.5 | 1.5 | 2.2 | |
Outlet of material | N | 24 | 24 | 44 | |
Power | Kw | 7 | 7 | 9.7 | |
Outer size | LXWXH | 5300X2400X3700 | 5300X2500X3700 | 5300X2600X3970 | |
Weight | T | 6.5 | 7 | 8.5 |
Applications
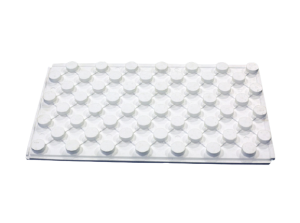
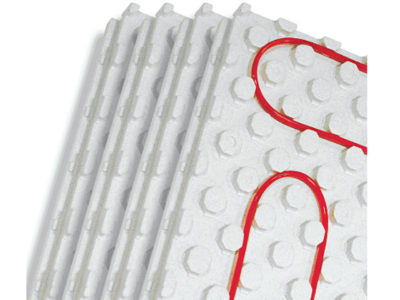
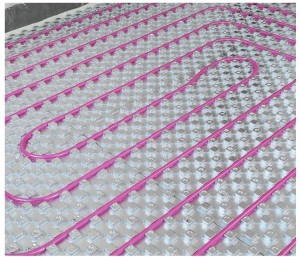
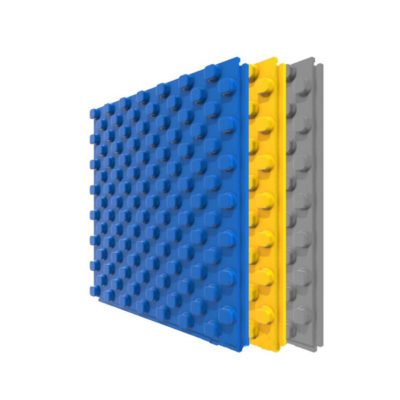
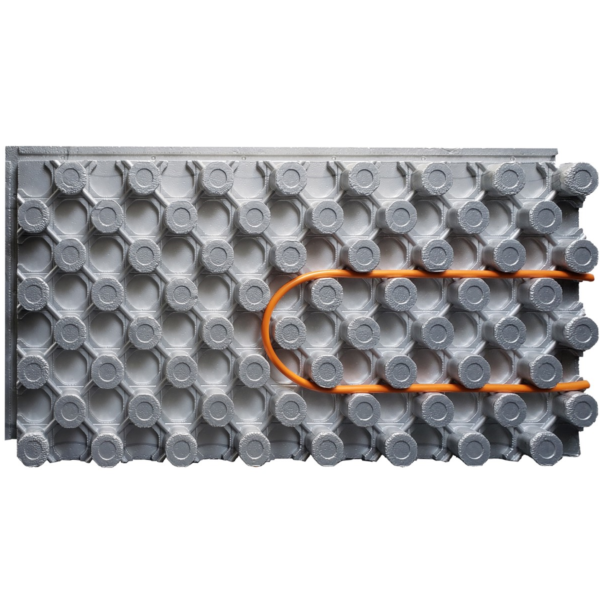
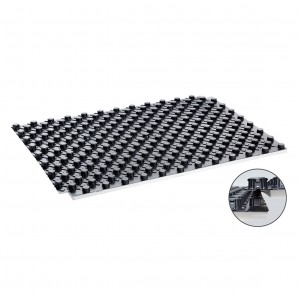