EPS High precise full auto batch expander machine
Main advantage
1. Fully automatic production.
2. Controlled by touch screen and PLC, easy to operate.
3. High output and save energy.
4. Exact density of foam beads.
5. Stable quality and less failure.
Main Features
Frequency spindle: the spindle rotation speed can be adjusted according to the raw material process,for ensuring that the material level can control the expanding weight precisely.
Steam system: adopt relief valve from YOSHITAKE,Japan, with high-precision drainage valve and filter to ensure steam pressure more stable.
Pressure control: international pressure sensor, German BATTON angle-seat valve and multi-valve exhaust system are used to ensure constant temperature and pressure expanding in the bucket, make sure the expanding process more stable and accurate.
Temperature control: The international temperature sensor and German BATTON steam and air dual proportional valve are used to control the temperature, so maintain the precise expanding temperature, for high -density expanding.
Weighing and feeding: electronic weighing for feeding, and the feeding weight is setup on the touch screen. The weighing devi ce will automatically weigh to achieve accurate feeding.
Material level control: adopt the vibration sensor from Korea to control expanding material level precisely, ensuring the uni form density of raw material particles.
Material level of fluidizer bed: the height of material level can be adjusted to ensure the aging effect of expanded particles. flap feeding device of fluidizer bed ensure the high efficiency of expanding particle.
Feeding Crushing device at bottom of fluidizer bed: to ensure convenient clean of fluidizer bed
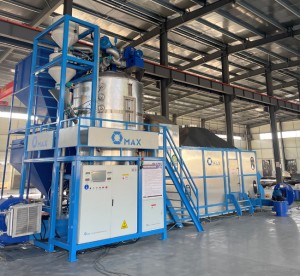
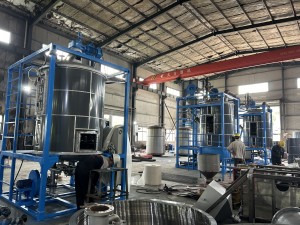
Technical Data
Item | Type | ||||
SPJ90 | SPJ110 | SPJ150 | SPJ160 | ||
Expansion Chamber | Diameter | Φ900mm | Φ1100mm | Φ1500mm | Φ1600mm |
Volume | 0.85m3 | 1.4m3 | 4.5m3 | 5.4m3 | |
Useable Volume | 0.6m3 | 0.9m3 | 3.2m3 | 4.5m3 | |
Steam | Entry | DN40 | DN50 | DN40 | DN100 |
Consumption | 2-4kg/cycle | 6-9kg/cycle | 15-18kg/cycle | 18-20kg/cycle | |
Pressure | 0.6-0.8MPa | 0.6-0.8MPa | 0.6-0.8MPa | 0.6-0.8MPa | |
Compressed Air | Entry | DN25 | DN25 | DN50 | DN40 |
Consumption | 0.3m3-0.4m3/cycle | 0.5m3-0.6m3/cycle | 0.5-0.6m3/cycle | 0.5m3-0.8m3/cycle | |
Pressure | 0.6-0.8MPa | 0.6-0.8MPa | 0.6-0.8MPa | 0.6-0.8MPa | |
Drainage | Drainage Port | DN100 | DN80 | DN100 | DN150 |
Condensate | DN40 | DN80 | DN40 | DN50 | |
Throughput | 13g/l 240kg/h | 12g/l 240kg/h | 12g/l 600kg/h | 12g/l 1500kg/h | |
18g/l 350kg/h | 15g/l 320kg/h | 15g/l 900kg/h | 15g/l 2000kg/h | ||
25g/l 480kg/h | 20g/l 430kg/h | 20g/l 1200kg/h | 20g/l 26000kg/h | ||
31g/l 590kg/h | 30g/l 600kg/h | 30g/l 1500kg/h | 30g/l 3100kg/h | ||
50g/l 720kg/h | |||||
Material Conveying Line | Φ150mm | Φ150mm | Φ150mm | Φ250mm | |
Power | 16.75Kw | 16.13Kw | 24.85Kw | 38.45Kw | |
Density | 12-90g/l | 12-30g/l | 12-30g/l | 12-30g/l | |
Density Tolerance | ≤±2% | ≤±3% | ≤±5% | ≤±3% | |
Overall Dimension | L*W*H | 4500*2000*4900 | 5600*3800*4530 | 4310*4150*5120 | 11000*2840
*6050 |
Weight | 2500kg | 3500kg | 5000kg | 8000kg | |
Room Height Required | 5000mm | 5000mm | 6000mm | 7000mm | |
Auto density-weighing system | optional | optional | optional | ||
Second expansion | include | optional |
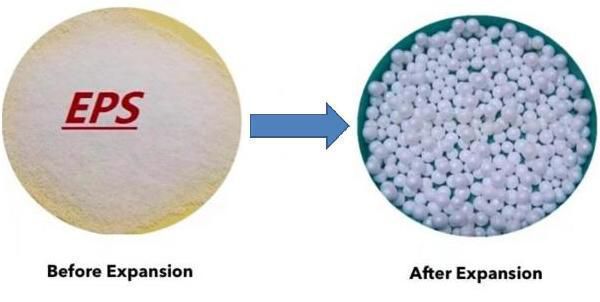
Products
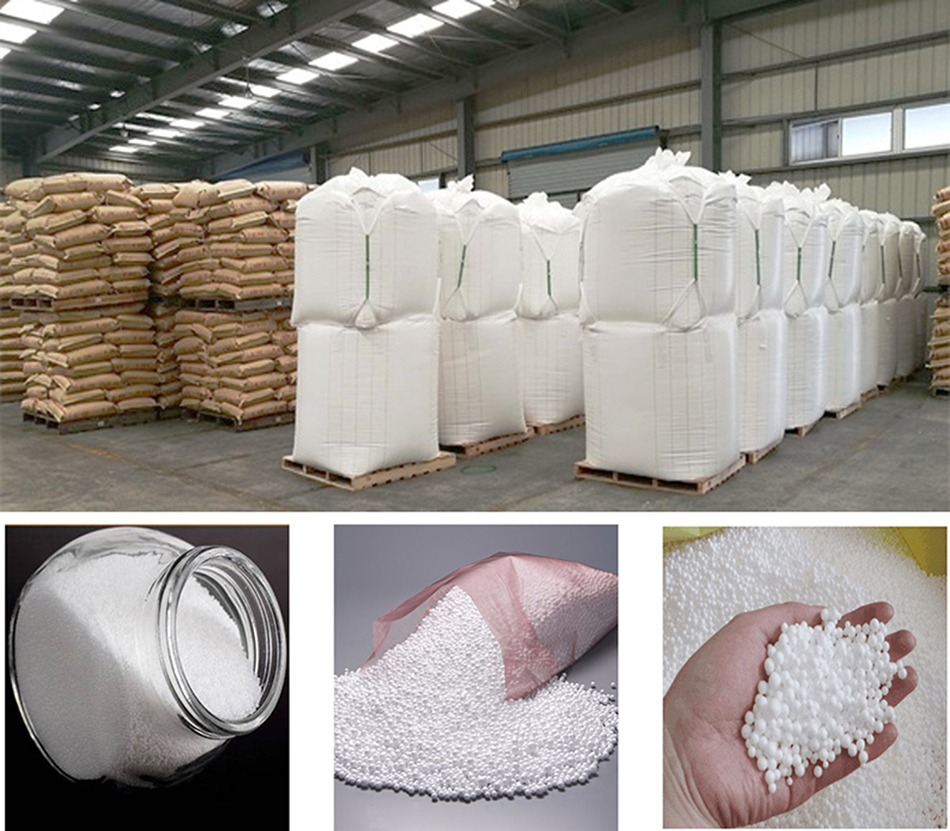